In high-pressure applications, choosing a durable rubber expansion joint is critical. This article answers common questions regarding high-pressure rubber expansion joints, helping you select the right product.
American standard high-pressure rubber expansion joints offer exceptional pressure resistance and durability, making them ideal for various industrial applications. In this article, you will learn about their lifespan, pressure ratings, and differences from metal expansion joints.
What is the pressure rating of a rubber expansion joint?
The pressure rating of a rubber expansion joint for pipe is a key factor when selecting the right product. Understanding the pressure capacity ensures safe operation in high-pressure environments.
Rubber expansion joints typically have a pressure rating of up to 300 psi or higher, depending on their design and materials. Choosing the right pressure rating prevents leakage and ensures long-term system stability.
For example, rubber expansion joint for concrete and rubber expansion joint for pipe may have different pressure requirements. You can refer to a rubber expansion joint catalogue to find products that meet your specific needs.
How long do rubber expansion joints last?
The lifespan of a rubber expansion joint depends on several factors, such as material quality, working environment, and maintenance.
Under normal operating conditions, a high-quality rubber expansion joint can last between 5 to 10 years or even longer, depending on the application and care.
Rubber expansion joints are a durable solution, especially in pipeline systems and concrete construction, such as rubber expansion joint for pipe and rubber expansion joint for concrete. Regular inspections and maintenance help extend their service life.
What is the difference between metal expansion joints and rubber expansion joints?
The main differences between metal expansion joints and rubber expansion joints lie in their materials, flexibility, and application environments.
Metal expansion joints are generally used in high-temperature, high-pressure environments, while rubber expansion joints are valued for their flexibility and corrosion resistance in low-pressure systems. Each type serves different purposes in industrial applications.
Rubber expansion joints, such as general rubber expansion joints, are more suitable for environments that require flexibility, vibration damping, and corrosion resistance. On the other hand, metal expansion joints, known for their strength, are ideal for extreme temperatures and pressures. Consult a rubber expansion joint catalogue to find the right product for your needs.
What are the disadvantages of bellows?
While bellows expansion joints offer advantages in specific situations, they also have some drawbacks.
The primary disadvantages of bellows include fatigue over time and higher maintenance costs, especially in high-pressure and high-temperature environments. The material’s rigidity can also limit flexibility compared to rubber alternatives.
Compared to rubber expansion joints, bellows lack the flexibility and vibration damping properties that are crucial in many applications. As a result, rubber expansion joint manufacturers often recommend rubber expansion joints for better performance in such environments.
What is the purpose of rubber expansion joints?
Rubber expansion joints serve a crucial role in absorbing vibration and compensating for thermal expansion in mechanical systems.
These joints effectively reduce stress and vibration in the system while accommodating changes in temperature that cause expansion or contraction. This makes them essential components in maintaining system integrity.
In pipeline systems, rubber expansion joint dimensions are critical to ensuring stability and durability. Properly sized and designed joints not only reduce maintenance costs but also enhance system longevity. Rubber expansion joint price will vary depending on the dimensions and application.
How much psi can rubber withstand?
The pressure resistance of rubber depends on the material quality and design. Selecting the appropriate product is essential.
Rubber expansion joints can typically withstand pressures of up to 300 psi, with specially designed joints capable of handling even higher pressures.
Depending on the rubber expansion joint dimensions and specific applications, the pressure resistance can vary. By consulting a rubber expansion joint catalogue, you can find products with different pressure ratings that meet your needs.
Summary:
Rubber expansion joints are flexible, durable products ideal for high-pressure systems. Choosing the correct size and pressure rating is essential to ensure reliable performance and system longevity.
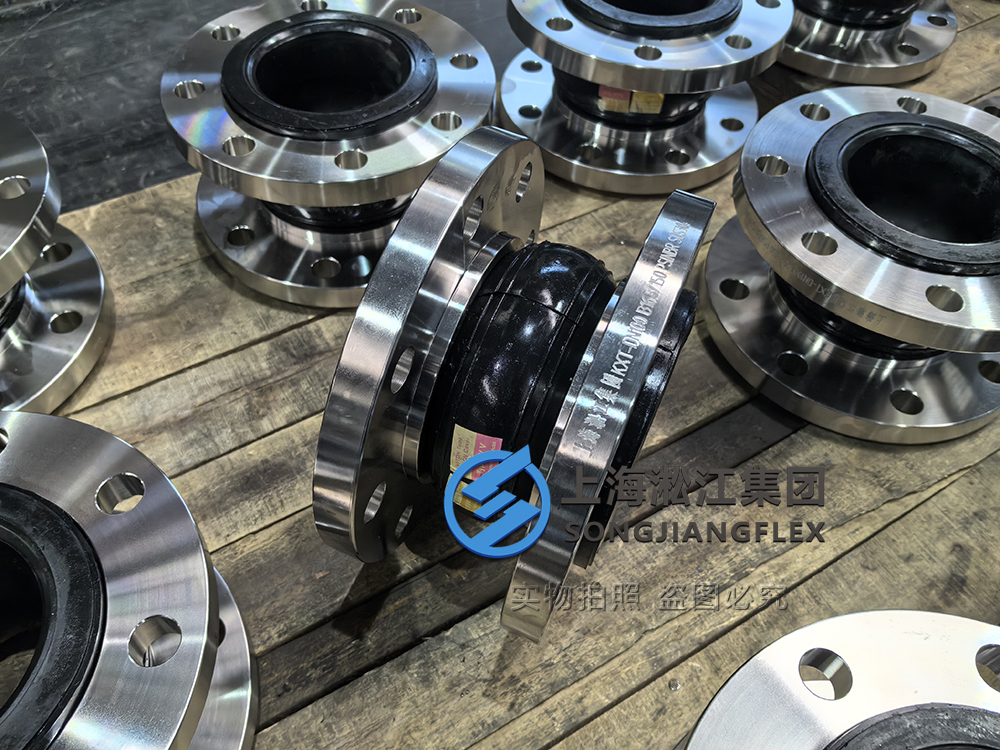
_cuva
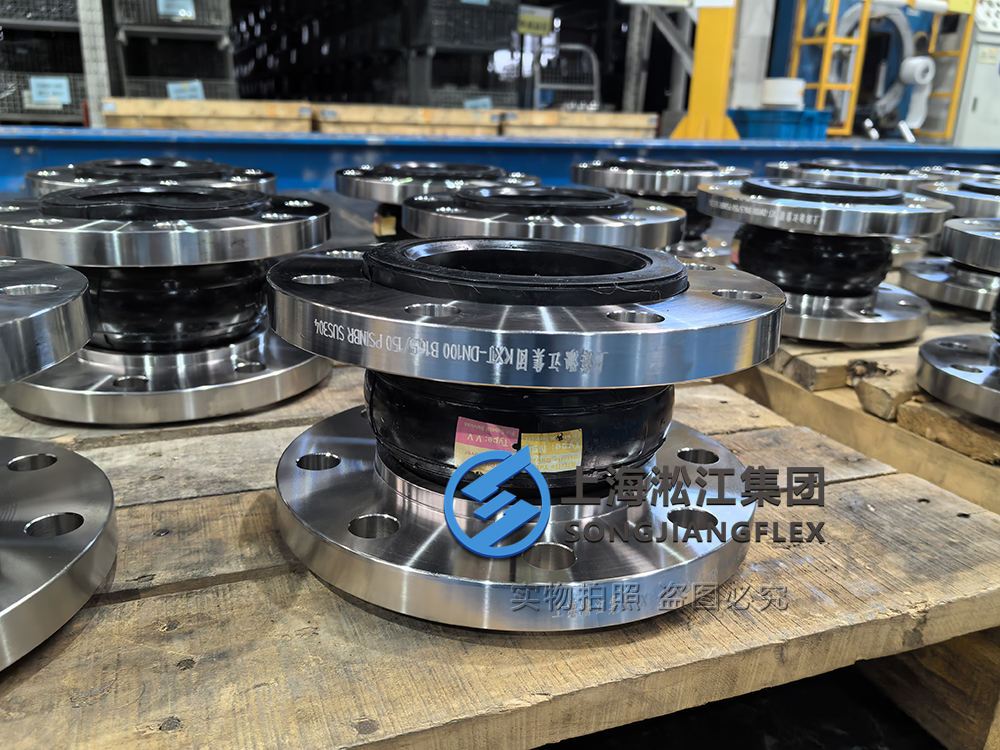
_cuva
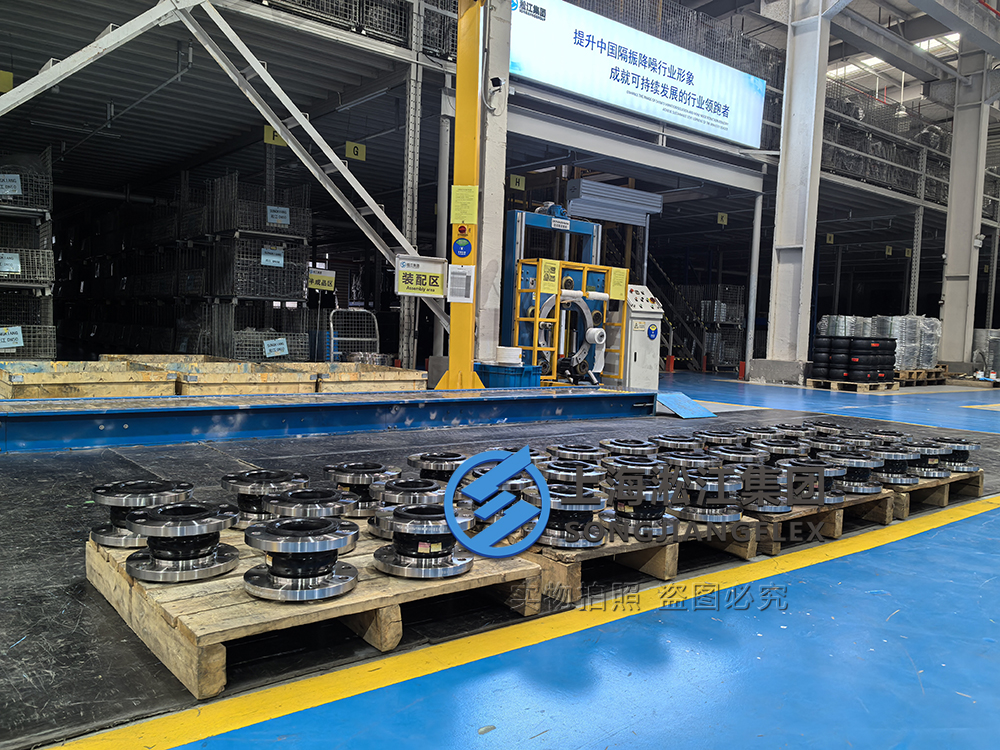
_cuva